Top Issue
Application technologies
Coating processes for zinc flake coating – these processes are used to apply the zinc flakes to your product
An anti-corrosion coating made of zinc flakes reliably protects small and large metal parts from environmental influences - and thus from corrosion. But for this to work, the zinc flakes must first be applied to the product. Read here about the processes that can be used and how the individual techniques work.
Overview of coating methods – These application techniques are available for our zinc flake coating
After successful pre-treatment, a golden future awaits your products. Or better: a silver one. After all, the primer of the zinc flake coating is silver. Individual colourings, for example in gold, only follow with the top coat – the topcoat.
The way the zinc flakes get onto your product can be quite different depending on the properties of the component.
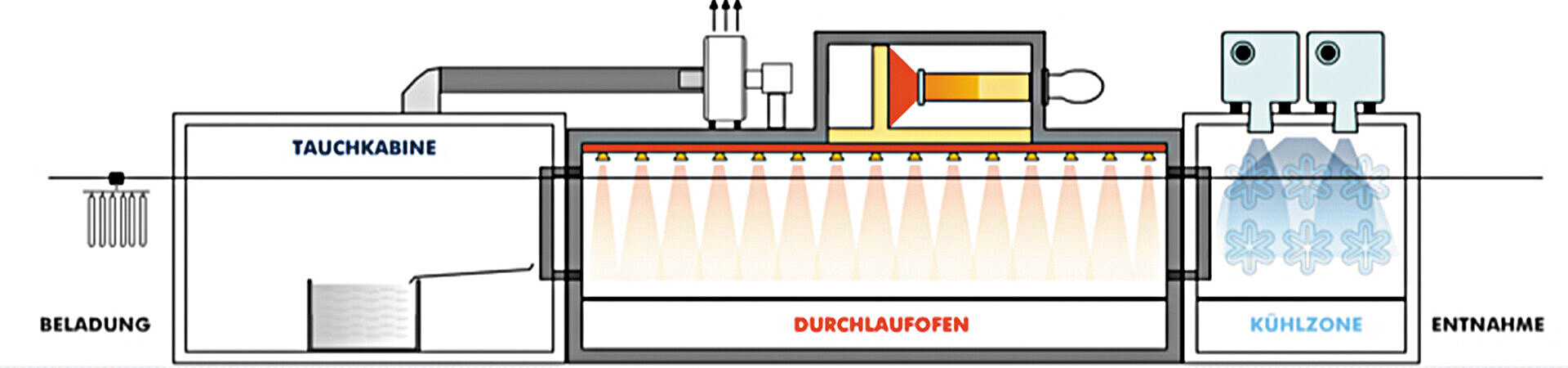
Coating by the dipping process
The application of the zinc flake coating by the dipping process is usually suitable above all for larger parts to be coated. For this purpose, the products are hung or placed in racks that guide them through the coating process.
Securely attached, they take a bath in the coating basin in the dipping cabin. In this way, every component is enclosed in the liquid coating right into the cavities. Even small-part products are thus reliably protected against rust - even on the inside.
After pulling the products out of the coating bath, the excess coating material simply drips off your products.
Still attached to the frame, the path now leads through a dryer. At individually set temperatures, the zinc flakes burn onto the component and become a personal protective armour. After the perfect dwell time in the oven, your components cool down to a predefined temperature in the cooling zone.
And then – if necessary – the process starts all over again. In another pass, your products receive further layers for individual protection.
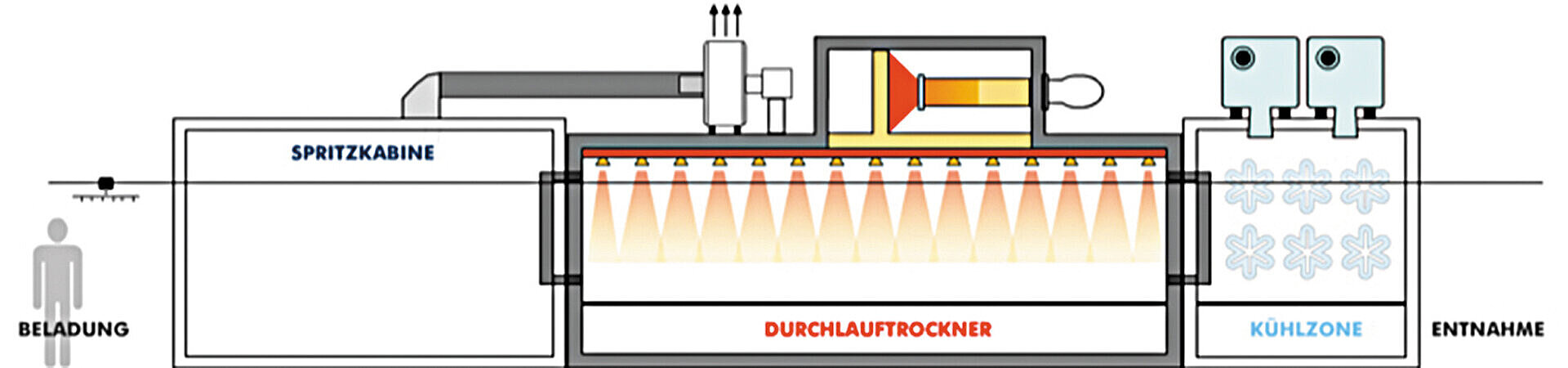
Coating in spray process
Applying the coating by spraying is also suitable, especially for larger parts. Similar to dipping, the products go through the process in racks that guide them through the individual steps.
Instead of being immersed in a basin, the zinc flakes are sprayed onto the parts in an extremely thin layer in this process. For this purpose, the spray nozzles automatically move along the parts to be coated at an individually programmed speed. The zinc flakes are atomised so finely that they lie tightly on the surface of the components.
Since the zinc flakes are sprayed on from the outside, this process is particularly suitable for products without cavities.
The wafer-thin layer of zinc flakes is cured in the continuous dryer – which is directly connected to the spraying chamber. At temperatures individually adapted to the products, the zinc flakes and the product surface bond firmly together and become one unit. In the following cooling zone, the products then reach normal temperature again.
As with dipping, the products can go through the process a second time if necessary for the individual requirements.
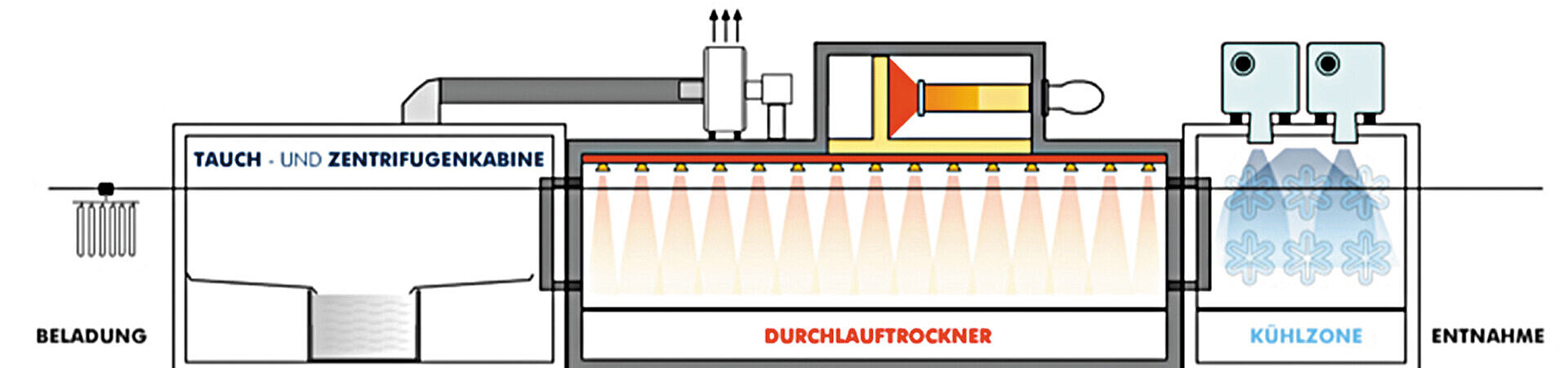
Coating by spin coating
Spin coating combines the advantages of several processes and thus enables even difficult components to be coated with a uniform, wafer-thin layer. It is particularly suitable for larger products.
With spin coating, too, the products are guided through the process on racks. Securely fastened, they are completely immersed in the liquid coating material, just like in dipping. The zinc lamellae completely enclose the components, even on the inside.
Excess material already drips back into the coating bath when it is pulled out. For even better coating results, the products are then centrifuged. Excess material is thus spun off.
As with dipping and spraying, the products then pass through the continuous dryer, in which the zinc flakes bond firmly to the product surface. In the cooling zone, the products cool down to normal temperature. If further layers are required, the process now starts again.
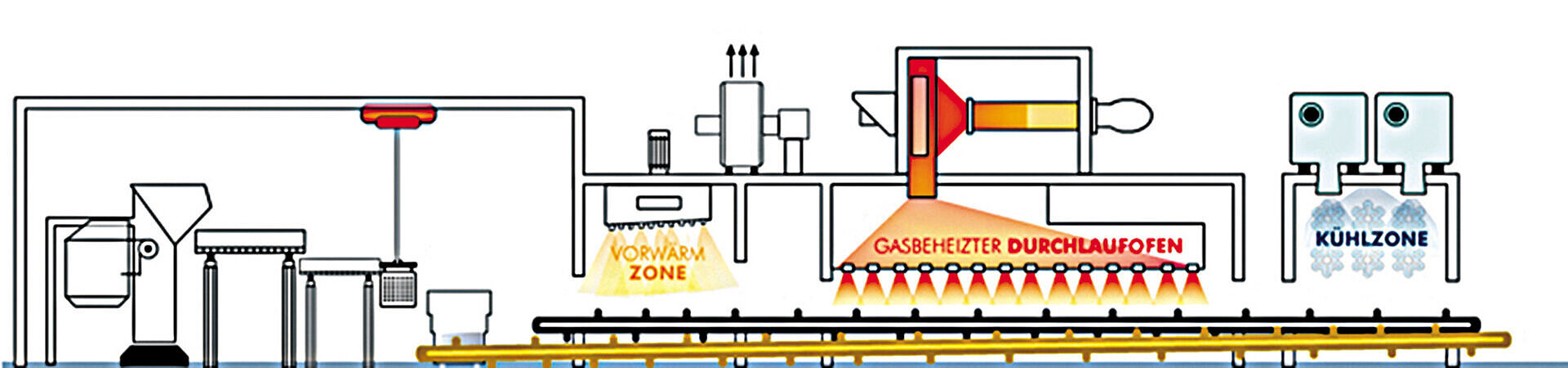
Coating by centrifugation
Small products and bulk material usually receive the zinc flake coating in a centrifugal process. In coating baskets, a large number of parts receive an even coating at the same time.
The parts to be coated are filled into the coating baskets and immersed with them in the coating material that is optimally matched to the products. The zinc flakes completely enclose the articles, even on the inside. The items are then centrifuged in the baskets. Excess material flings off the products and leaves an even surface.
For drying in the continuous oven and cooling in the cooling zone, the parts are emptied from the coating baskets onto a conveyor belt. Further passes are also possible in this process to achieve a product-specific coating.
Best coating results with microcor
microcor is the zinc flake coating that really suits the product. Every parameter of the coating is individually adapted to the requirements of the products. The coating is carried out exclusively in specially developed plants that can meet the requirements in every respect. The coating material is also exclusively of the best and strictly controlled quality and is prepared individually for each product.
Eibach Oberflächentechnik GmbH
Golsberger Str. 3
D-58513 Lüdenscheid
+49 2351 9546-0
+49 2351 9546-99
I agree to the processing of my data for the purpose of contacting me.